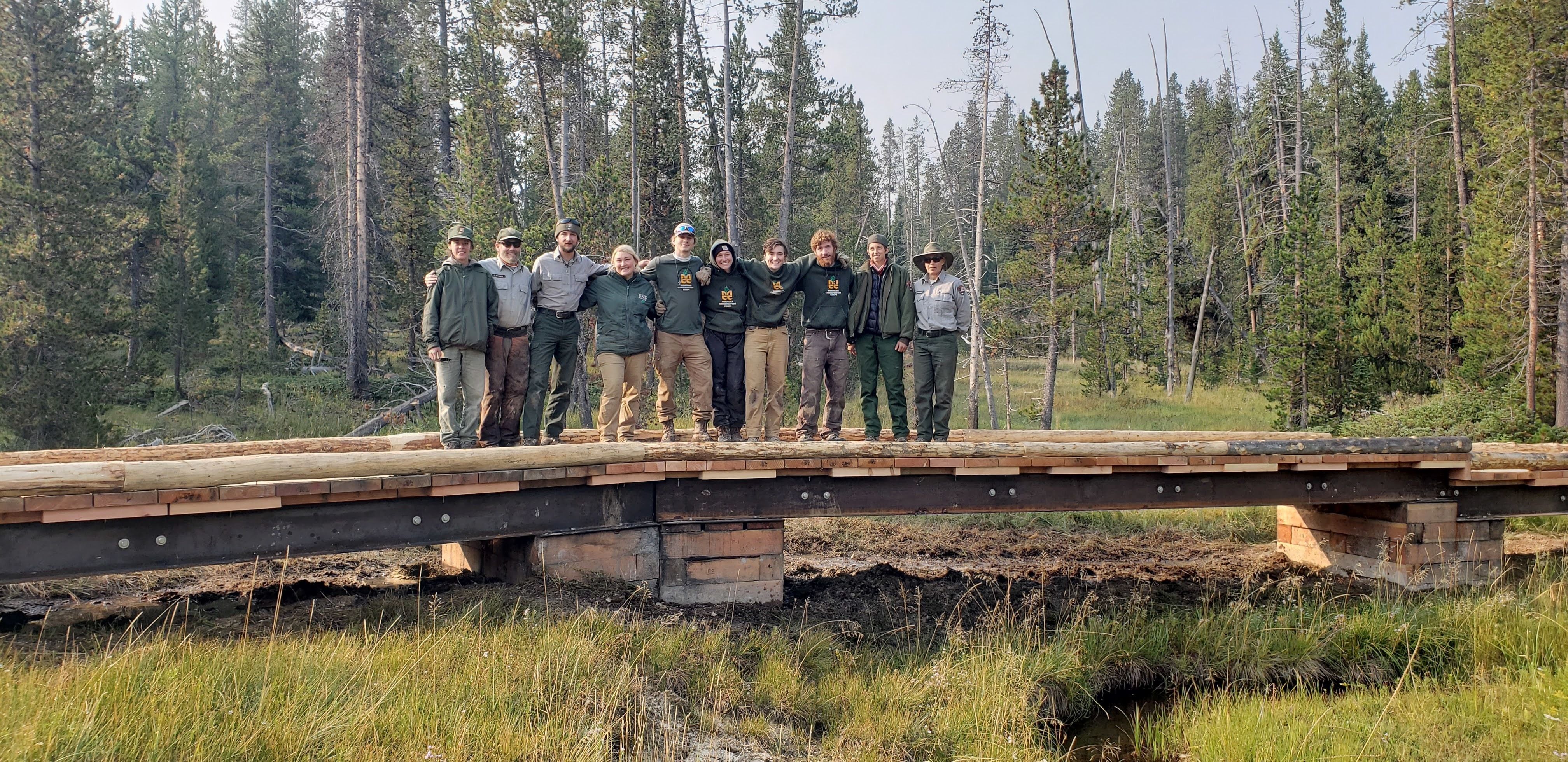
This project, which spanned two separate hitches with 12 workdays over three weeks, was by far the most challenging hitch we have had as a crew this season. We had the amazing opportunity to help build the longest high beam bridge in all of Yellowstone’s history. This 152-foot bridge, which included a difficult turn and uneven terrain, allowed our crew to learn about building, working with dangerous power tools, carrying heavy materials safely, and it even taught us how to plan accordingly for backcountry hitches.
On the first workday of this project on August 4th, we began by ripping up the old wooden bridge that was in place along the Bechler Trail (which is utilized by a lot of CDT hikers going to either Mexico or Canada). We learned how to safely take out old rusted nails and screws from bull rails (large logs) and waterlogged planking. After dispersing the old wood, abutments were made by making perfectly square wooden structures connected with allthread. We learned how to properly measure and square these abutments, which would be used to connect the deck of the bridge to the ground, helping to support the bridge’s weight both vertically and horizontally.
Once the ground was dug out and the first two abutments were placed in, they needed to be perfectly level. We then carried three 400 lb steel beams and placed them on metal plates on top of the abutments. We learned how to screw the beams into place, how to mark the steel plates for drilling, and eventually, we all had a chance to drill through the steel into the wood with a magnet drill. Once the steel was drilled, large screws were put in place and the beams were secured. The final step of this process is attaching wooden “scabs” (wooden 2x4s) on top of the steel beams and then screwing on the decking on top of the scabs. There were seven abutments made for this bridge, all different sizes due to the varying terrain, so this entire process was repeated for each section of the bridge we put in, allowing our whole crew to adjust to this process and get quicker and more efficient by the day.
We also learned how to limb and peel logs to be used as bull rails for the sides of the bridge. Overall, this project tested us mentally, physically, and emotionally as we all battled the cold, wet mornings in Yellowstone National Park. We got to work with incredible park service individuals and made long-lasting connections and memories as we all suffered the harsh conditions together. Hopefully we will visit this bridge in the following years and appreciate all of the hard work we were able to accomplish by working as a team and supporting each other through the toughest days.